工业革命是现代制造业的起点,核心是产品的规模化生产。上个世纪,电脑的发明让制造业实现了数字化,2000年开始的互联网革命,让数据能够彼此连接,进一步提升了数据利用的效率。当我们分析产业趋势的时候,思路要从需求出发,找到能够满足需求的技术,最后分析哪些企业在满足市场需求上取得了竞争优势。制造业的核心需求总结出来其实就是三条:可管可控、提质降价和个性制造。可管可控是一个工厂运行的基础,需要对设备工作状况、产线运转状态、库存等信息有实时的了解,可在出现异常状态前,就提前进行维护。技术上主要通过布设大量的传感器和摄像头实现。其次是优化生产效率,也就是提质降价。主要的技术实现手段是大量运用机械臂和机器人替代人工。最后是个性化制造,这个环节的难点是,如何同时满足个性化和规模化的生产。目前的生产线之所以效率高,是因为通过高度重复的流程,能快速生产标准化的产品,但产线的变化永远跟不上产品的变化。以上我们总结了制造业的三大核心需求,和分别对应的技术实现手段,但有一项技术可同时从这三个方面对工厂进行优化,让它具备持续更新迭代的能力,这就是数字孪生。快速迭代本来是软件产品的专利,因为更新维护成本很低,可以通过快速试错,根据用户的反馈不断优化自己的产品。
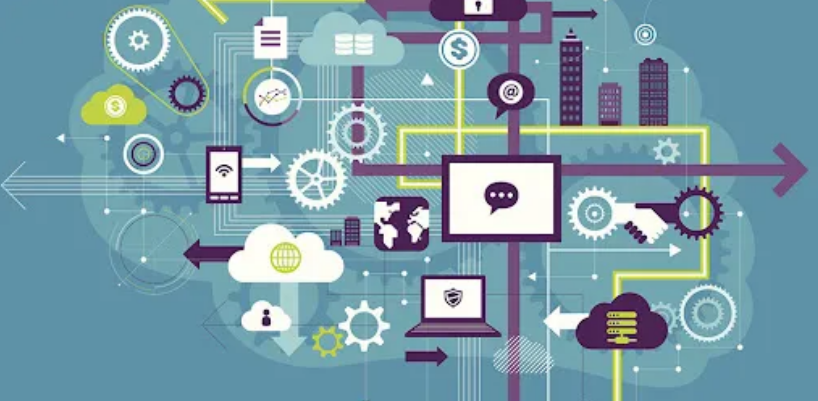
但这种能力在硬件产品上就难以实现,因为造出一个硬件产品原型就得花不少功夫,更别说根据用户使用后的反馈进行快速优化了,所以硬件产品的更新换代通常会慢很多。不过,数字孪生技术的出现将根本性的解决这个问题。因为当我们能在高度仿真的虚拟环境中模拟硬件的运行,就能测试各种不同的改动,然后根据测试结果进行优化,最后再生产出优化后的产品。我们经常举的例子是自动驾驶汽车,当我们把汽车模型、传感器参数等等纷纷数字化之后,让数字化的汽车在仿真环境中训练自动驾驶能力,最后再把训练好的算法输回汽车里,那么这台现实中的汽车就具备了优化后的自动驾驶能力。再往前想一步,如果硬件产品可以实现持续迭代,那么生产硬件产品的工厂可以吗?其实有不少企业已经在尝试了,例如宝马和英伟达合作,利用其Omniverse平台,打造了一个数字孪生汽车生产车间,里面不但高度还原了产线的流程和机械结构,还包括工人、机器人等,几乎涵盖了现实中这座工厂的所有元素。
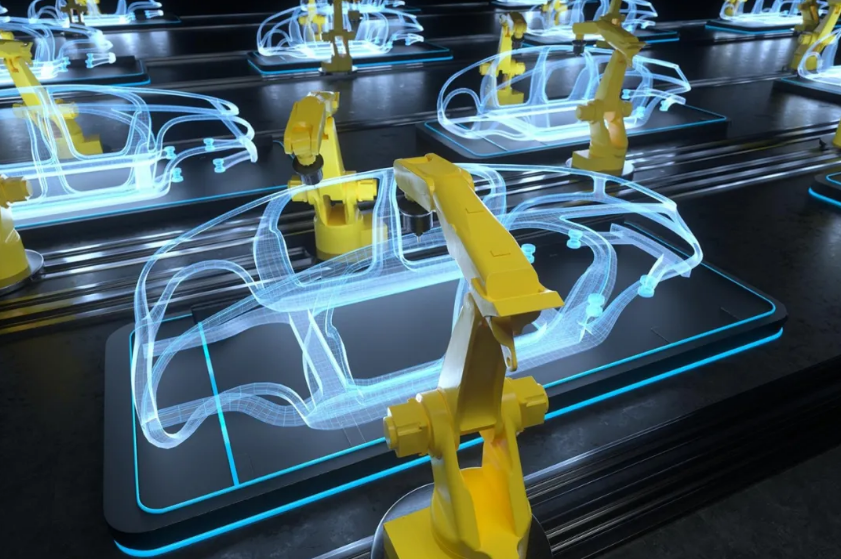 虚拟化带来的好处就是,每当工厂中的设备需要更新时,都可以先在仿真环境中进行测试优化,或者对新的设备进行训练,使其能快速适应真实工厂的环境。宝马公司的董事Milan表示,这座数字孪生工厂可将宝马的生产规划效率提高30%。
美国著名设备制造商通用电气公司,已经将数字孪生作为公司的长期战略之一,构建了超过150万个数字孪生体,包括飞机引擎、海上石油钻井平台、风力发电厂等等。
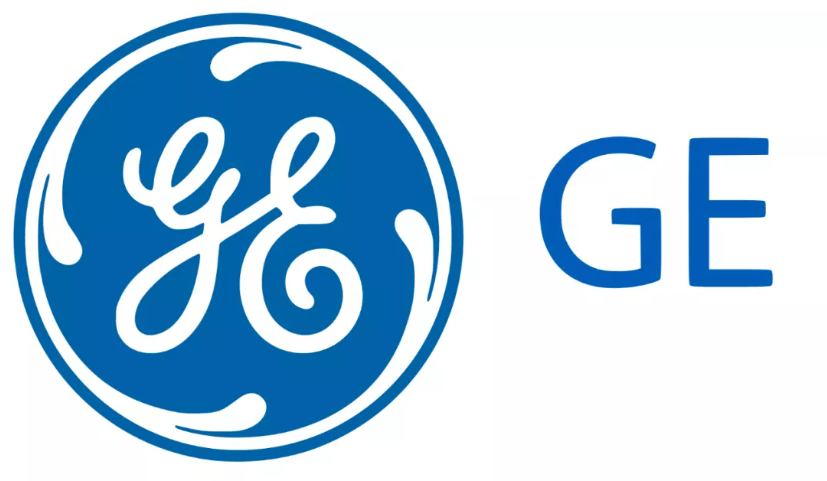 可以预见,数字孪生技术将是制造业从自动化到智能化转型的重要技术之一,未来对工厂的设计规划也会从可持续升级迭代的角度重新展开。
|